Impact of the Baltimore Bridge Collapse
The recent collapse of the bridge in Baltimore has caused significant disruptions to the automotive industry’s supply chain. With the bridge being a crucial artery for transporting vehicles and parts, automakers have been forced to find alternative routes and modes of transportation to keep their operations running smoothly.
The sudden closure of the bridge has led to delays in deliveries and increased transportation costs, posing challenges for automakers as they work to meet customer demand and maintain production schedules.
Strategies for Managing Disruptions
In response to the shipping disruptions caused by the bridge collapse, automakers have implemented various strategies to mitigate the impact on their supply chains. One approach is to reroute shipments through alternative ports and transportation networks, although this may result in longer transit times and higher costs.
Some automakers are also exploring the use of air freight and expedited shipping services to expedite deliveries and minimize delays. Additionally, manufacturers are working closely with suppliers and logistics partners to identify bottlenecks and develop contingency plans for future disruptions.
Lessons Learned and Future Preparedness
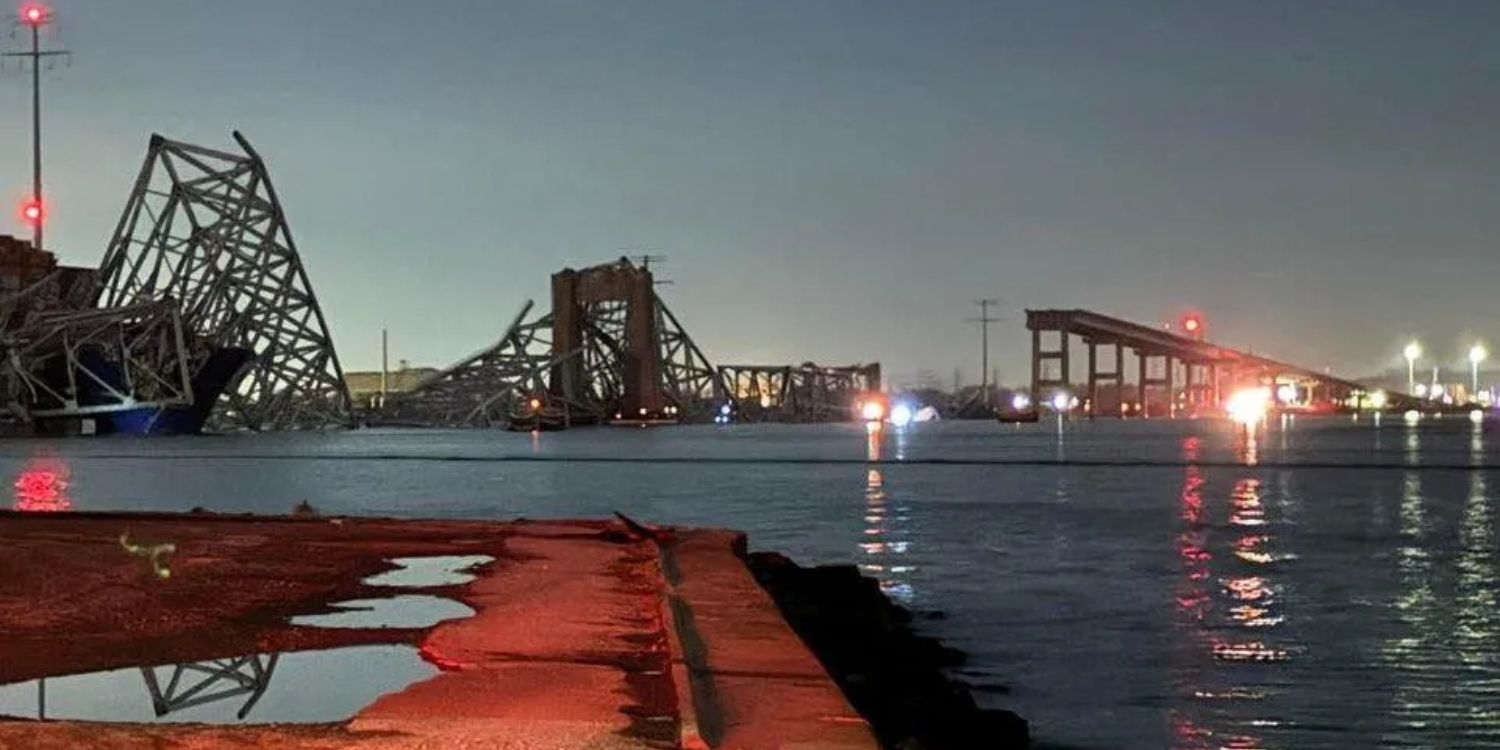
The Baltimore Bridge collapse serves as a reminder of the vulnerability of the automotive industry’s supply chain to unexpected events. Moving forward, automakers are taking steps to enhance resilience and preparedness in the face of potential disruptions. This includes investing in digital technology and data analytics to improve visibility and transparency across the supply chain, as well as diversifying transportation routes and modes to reduce reliance on a single point of failure.
By learning from the challenges posed by the bridge collapse and implementing proactive measures, automakers can better position themselves to withstand future disruptions and ensure the continued flow of vehicles and parts to market.